MESH TIDYING
Right you've finished your mesh now comes the tidying up! No matter how careful
we are in constructing our mesh certain errors always pop up during construction that are overlooked and might cause problems later. I'm aiming to provide some general guidelines for construction and some tips for tidying up - these tips are also extremely handy when handling Conversion from other file formats.
First I will deal with the Point Multiplication Problem. As we all know Pointnumbers are a limiting factor of all the earlier versions of LightWave - only now in Version 6 and above has it been done away with. A common problem I have seen people face is this one. They have made a tube with various sections that are raised, they still want sharp definition of the edges of these sections; but with a smoothing angle of 89.5 degrees(LightWave's default) which is usually used for tubes we get this result:b
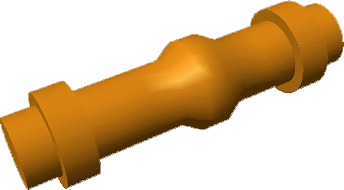
Now the most common technique I have seen used to eliminate this problem it to cut out the offending section and then paste it back in again like so
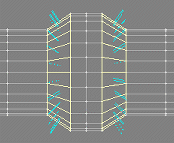
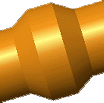
As you can see this does solve the problem - but what is the major drawback with this technique? Well you have effectively doubled all the point counts in these areas.
The result is that you will now have 192 points where there should really only be 96! This might not be a problem on small meshes - but just imagine what happens when you mesh has many antennas and gun barrels - it doesn't take a genius to figure out that soon you will be in the realms of multi object ships that need to be assembled in Layout! So.. The question is - how do we rectify this?
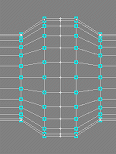
Well let's not cut and paste the offending object section out at all - ensure that your tube has an absolute minimum of 24 sides - personally I always use 36 sides for everything but the smallest pipes and tubes that will never be that noticeable. Poly's? Well LightWave can handle them - Points? - Start a new object!! Now instead of cutting and pasting lets reduce the smoothing angle to just 60degrees and see what happens?
well - the smoothing error is still there
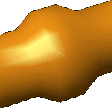
what about 40 degrees?
nope still there!
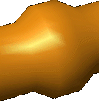
what about 30 degrees?
would you look at that - it's gone! BUT the tube now has a slight faceted look to it - very subtlebut there - check the highlight out and compare to below - and that's because it is a 24 sided tube
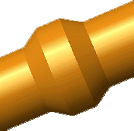
let's use a 36 sided tube which will let us use a 40 degree smoothing angle because of the greater number of sides:
So now you know why I always use smoothing at approximately 40 degrees and 36 sides for tubes - it saves on the points baby
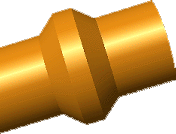
Next we move onto a related but dissimilar problem that many encounter - you have Lathed an almost flat but yet curved surface - for example the top of a saucer hull - and now you want to put raised panels and recessed windows in - lets look at what it's like with a default smoothing angle of 89.5 degrees.
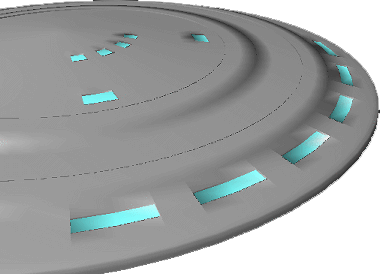
As you can see the smoothing errors on the raised panels and the windows are awful - let's drop the smoothing down to 60 degrees and see what happens.
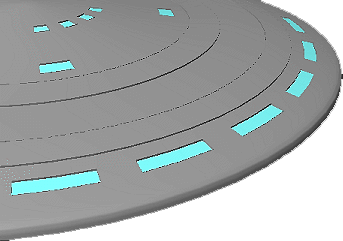
There it's gone - but sometimes you will encounter a mesh that will still have smoothing errors at angles as low as 40, 30 or even 20 degrees! But remember though that you can set the smoothing on relatively flat surfaces to just 10 degrees and make the saucer look smooth and thus eliminatesmoothing on any windows and raised edges. Remember that -- 10 degrees.
Now with that out of the way - which will help you out a lot in the long run believe me....first we move onto tidying up the final construction. You can either do these steps on the whole mesh if it is a relatively small one or section by section for large complicated meshes.
First check that there are no points that are not connected to any polygons
using the requester and checking in the appropriate box.
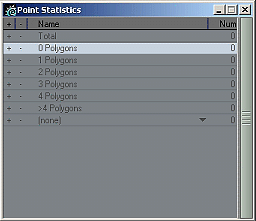
Now sometimes with reduce poly functions, point merge, point weld - and other functions you will be left with poly's that consist of either one or two vertices - these are for all intents and purposes useless and should be selected and then cut away - they do have their uses such as hair with a medium or large polygon line size in layout for instance; but in the general scheme of things just get rid of the little things!
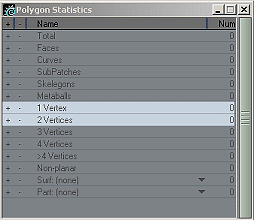
Next select the non planar polygons - these are basically poly's that are curved and always have more than 3 points - they can and sometimes do cause rendering errors in layout as they tend to give the rendering engine a little headache. Select them - there may be many - so deal with areas one at a time.
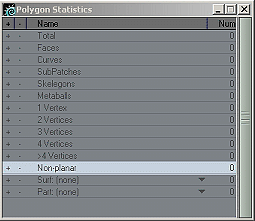
There it's gone - but sometimes you will encounter a mesh that will still have smoothing errors at angles as low as 40, 30 or even 20 degrees! But remember though that you can set the smoothing on relatively flat surfaces to just 10 degrees and make the saucer look smooth and thus eliminatesmoothing on any windows and raised edges. Remember that -- 10 degrees.
Now with that out of the way - which will help you out a lot in the long run believe me....first we move onto tidying up the final construction. You can either do these steps on the whole mesh if it is a relatively small one or section by section for large complicated meshes. First check that there are no points that are not connected to any polygons using the requester and checking in the appropriate box.
Now the simplest way to get rid of a non planar poly is to triple it
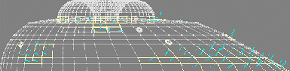
leaving this result - all well and done!
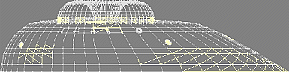
- but sometimes it can leave you with loads of little triangular polygons - especially around multi point windows
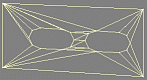
The trick here is to select polygons wisely and run the merge polygon macro then check for non planar again - if any - triple and repeat - you'll end up with a nice poly layout in the problem area with no non-planar polygons.
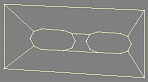
An important thing to bear in mind is that Layout can cope with non-planar quite happily sometimes - so check in a render and animation first to see which are the real problem areas and then rectify just them if necessary.
Last thing to do now is to check that there are no polygons that coexist exactly in the same place - these are a nightmare for the render engine - do it by simply pressing the unify button - this tool will find the offending polygons and delete them. - easy eh?
There is another check and that is for alignment - but you should always attempt to only ever use double sided polygon surfaces where they are absolutely necessary and ensure your vertices face the correct way.
Sometimes conversions can have ridiculous polygon facing setups and even then the Align polygons function won't have much effect on them - so that check is really up to you in the end.
I hope this helps you all out. Above all - Have fun!!